Detailed Welding Inspection Service for High-Performance Welding
Detailed Welding Inspection Service for High-Performance Welding
Blog Article
Understanding the Various Kinds of Welding Techniques and Providers Readily Available
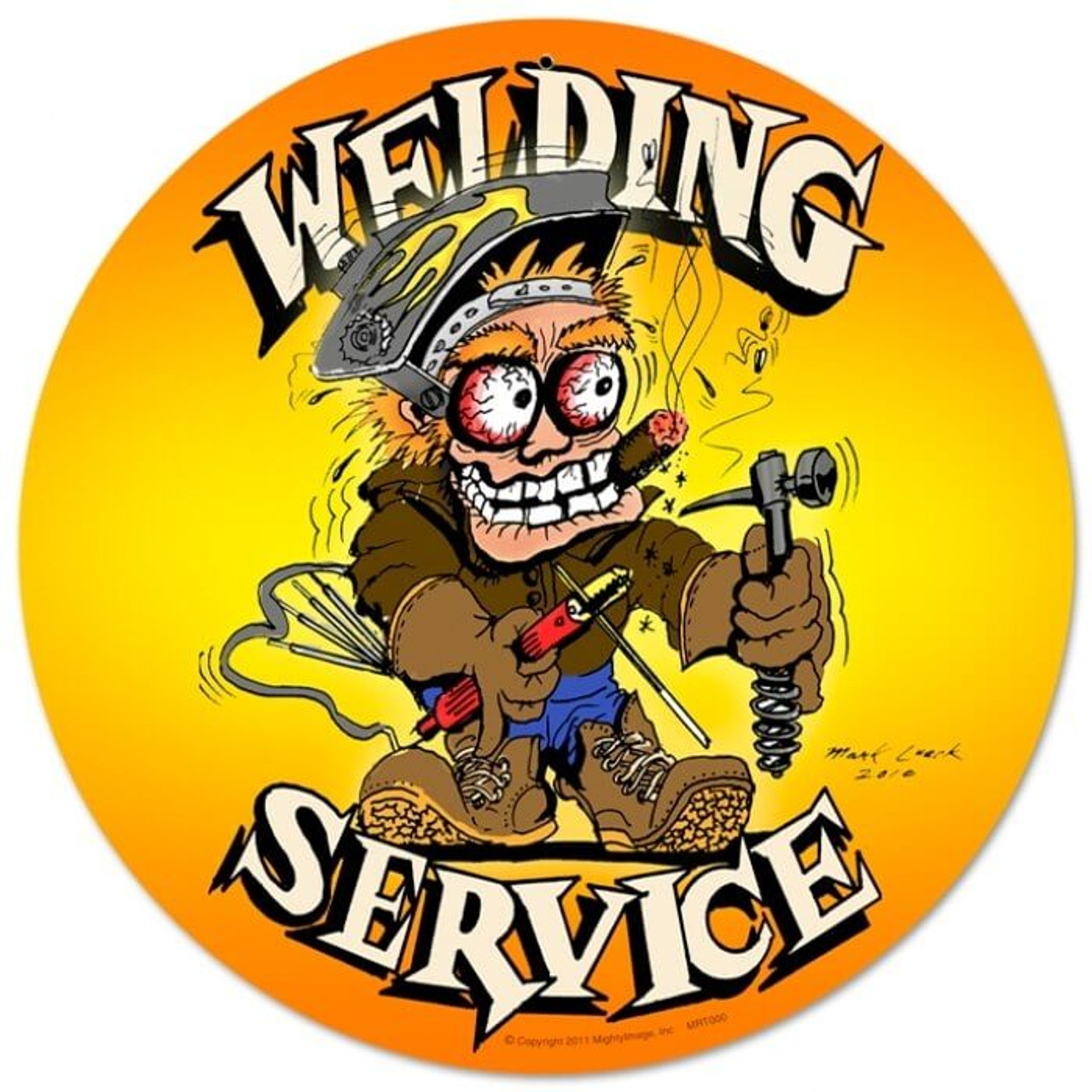
Introduction of Welding Strategies
Welding methods encompass a varied range of techniques used to join materials together permanently. One common method is arc welding, which entails producing an electrical arc between an electrode and the base material to melt and fuse them with each other. This method is versatile and can be made use of with different metals, making it among one of the most widely used welding procedures.
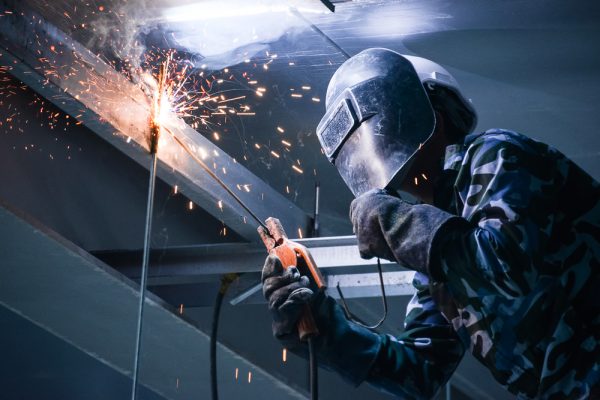
Furthermore, TIG welding, or Gas Tungsten Arc Welding (GTAW), is a specific and tidy welding method that uses a non-consumable tungsten electrode to develop the weld. TIG welding is generally used for thinner products and gives excellent control over the welding process. Overall, understanding these various welding methods is necessary for selecting one of the most ideal approach for various tasks.
Frequently Used Welding Approaches
A range of frequently utilized methods are utilized in the field of welding to successfully sign up with products with each other. One of one of the most commonly made use of strategies is Gas Metal Arc Welding (GMAW), likewise referred to as MIG welding. This approach makes use of a cord electrode that is fed through a welding weapon, together with a protecting gas to shield the weld from impurities in the air. One more common approach is Protected Metal Arc Welding (SMAW), or stick welding, which utilizes a flux-coated electrode to produce the weld. Tungsten Inert Gas (TIG) welding is preferred for its accuracy and convenience, using a non-consumable tungsten electrode to create the weld. Flux-Cored Arc Welding (FCAW) is frequently used in industrial setups due to its high welding speed and portability. Furthermore, Immersed Arc Welding (SAW) is excellent for developing deep welds on thick products. These typically used welding methods satisfy different needs and materials, giving choices for different welding applications.
Advanced Welding Solutions
Building upon the foundation of frequently used welding approaches, the world of innovative welding services encompasses advanced strategies and technologies that press the boundaries of accuracy and effectiveness in product signing up with procedures. Advanced welding solutions frequently involve specialized techniques such as laser welding, electron beam of light welding, and rubbing mix welding. Laser welding makes use of a highly focused beam to specifically sign up with steels with very little heat-affected zones, making it suitable for complex or fragile parts. Electron light beam welding, on the various other hand, utilizes a high-velocity electron light beam to produce deep weld penetrations in materials like aerospace alloys or different steels. Rubbing stir welding, a solid-state joining procedure, makes it possible for the welding of products that are testing to fuse using standard methods, like aluminum and copper. These innovative techniques provide boosted control over the welding procedure, causing more powerful, a lot more resilient welds with minimized distortion and boosted overall quality.
Specialized Welding Strategies

An additional specialized welding method is laser light beam welding, where a very concentrated light beam of light is utilized to sign up with steels with minimal heat-affected areas and distortion. This approach is typically utilized in markets needing high precision and sanitation, such as electronic devices and clinical device production. Additionally, eruptive welding is an one-of-a-kind method that utilizes controlled explosives to bond dissimilar steels together, developing strong and reliable joints. These specialized welding techniques showcase the variety and innovation present in the field of welding, supplying remedies for a variety of industrial applications.

Picking the Right Welding Process
With various welding strategies available, it is vital to think about factors such as the type of metal, thickness, joint style, and desired end outcome when selecting the best welding process. Amongst the common welding approaches are Gas Metal important link Arc Welding (GMAW), Protected Metal Arc Welding (SMAW), Gas Tungsten Arc Welding (GTAW), and Flux-Cored Arc Welding (FCAW) GMAW, also known as MIG welding, is ideal for welding slim to thick steels and is functional in various settings.
Final Thought
Finally, understanding the different kinds of welding techniques and solutions offered is vital for selecting the right method for a details task. By knowing the frequently utilized welding approaches, progressed welding services, and specialized strategies, people can make informed choices to ensure the success of their welding tasks. It is important to consider factors such as products, job needs, and budget plan when choosing the most ideal welding procedure.
From traditional techniques like stick welding to sophisticated processes such as laser welding, the globe of welding supplies a multitude of choices for signing up with metals with each other.Additionally, TIG welding, or Gas Tungsten Arc Welding (GTAW), is a clean and specific welding technique that makes use of a non-consumable tungsten electrode to develop the weld. Advanced welding solutions usually involve specialized methods such as laser welding, electron beam of light welding, and friction mix welding. Among the usual welding techniques are Gas Metal Arc Welding (GMAW), Shielded Metal Arc Welding (SMAW), Gas Tungsten Arc Welding (GTAW), and Flux-Cored Arc Welding (FCAW) By being conscious of the frequently utilized welding techniques, progressed welding solutions, and specialized techniques, people can make educated decisions to guarantee the success of their welding jobs.
Report this page